品牌ANSV安信防爆
防爆箱如何生产
防爆箱的生产是一个较为复杂的过程,需要严格遵循相关标准和规范,以下是一般的生产流程:
设计与规划
需求分析:与客户沟通,明确防爆箱的使用环境、防爆等级、电气参数、外形尺寸、安装方式等具体要求,同时根据使用场景和防爆要求,确定防爆箱的结构形式,如隔爆型、增安型等。
图纸设计:利用的 CAD 或 SolidWorks 等设计软件,绘制防爆箱的三维模型和详细的二维工程图纸,标注出各个部件的尺寸、公差、材质、表面处理要求等技术参数。
原材料采购
材质选择:根据设计要求,选择合适的原材料,如铸铝合金、不锈钢、碳钢等用于制造外壳,同时采购具有相应防爆等级的电气元件、密封材料、紧固件等。
质量检验:对采购的原材料进行严格的质量检验,检查材料的规格、性能、外观等是否符合要求,确保原材料的质量合格,如检查铝合金材料的化学成分、机械性能是否符合标准。
外壳制造
铸造或机加工:如果采用铸铝合金材质,通过铸造工艺将熔化的铝合金倒入预先制作好的模具中,冷却成型后得到外壳毛坯;对于不锈钢或碳钢材质,常采用机加工的方式,通过切割、冲压、折弯、焊接等工艺,将板材加工成所需的外壳形状。
表面处理:对制造好的外壳进行表面处理,以提高其耐腐蚀性和美观度,如采用喷涂、电镀、氧化等处理方法,在外壳表面形成一层保护膜。
内部电气系统安装
元件安装:根据设计图纸,将各种防爆电气元件如开关、插座、继电器、仪表等安装在外壳内部的位置,使用螺栓、螺母等紧固件将元件固定牢固,确保安装位置准确,电气间隙和爬电距离符合标准要求。
布线与连接:按照电气原理图进行布线,使用符合防爆要求的电缆或电线,采用防爆密封接头等连接件进行连接,确保线路连接可靠,绝缘性能良好,同时对布线进行整理和固定,避免线路混乱和相互干扰。
密封处理
安装密封件:在箱门与箱体的结合面、电缆引入孔等部位安装密封垫圈、密封胶条等密封件,确保密封件安装位置正确,无扭曲、变形等现象,良好的密封效果。
涂抹密封胶:在一些密封件无法完全密封的部位,如缝隙、孔洞等,涂抹适量的密封胶,进一步增强密封性能,防止易燃易爆气体或粉尘进入箱内。
防爆性能测试
压力测试:对防爆箱进行压力测试,以检验其外壳的强度和密封性,通常采用水压或气压试验,将一定压力的水或气体充入箱内,保持一段时间,观察箱体是否有泄漏、变形等现象。
电气性能测试:使用的测试设备,对防爆箱的电气性能进行测试,包括绝缘电阻测试、接地电阻测试、耐压测试等,确保电气系统的安全性和可靠性。
防爆性能检验:按照相关防爆标准,对防爆箱的防爆性能进行全面检验,如检查隔爆接合面的间隙、宽度是否符合要求,电气元件的防爆标志是否正确等。
装配与包装
整体装配:将经过测试合格的各个部件进行整体装配,安装箱门、把手、锁具、观察窗等附件,确保各个部件装配到位,功能正常,然后对防爆箱进行清洁,去除表面的灰尘、油污等杂质。
包装发货:根据客户需求和运输要求,对防爆箱进行包装,一般采用木箱、纸箱等包装材料,确保在运输过程中防爆箱不受损坏,然后按照客户的地址发货。
在整个生产过程中,质量控制贯穿始终,每一道工序都需要进行严格的检验和测试,确保防爆箱的质量和性能符合相关标准和客户要求。
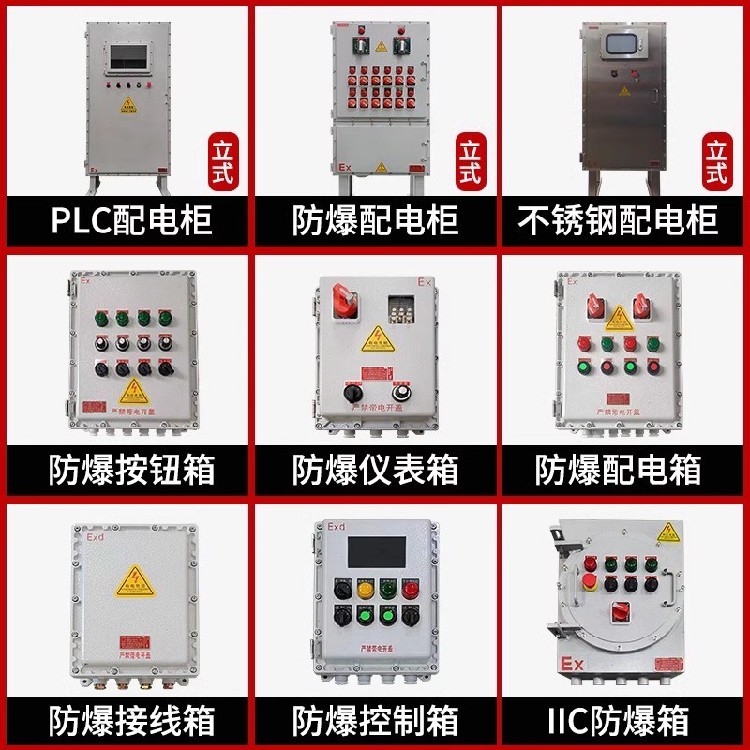
防爆箱如何设计
防爆箱的设计需要综合考虑多方面因素,以确保在危险环境中能安全可靠地运行。以下是防爆箱设计的主要要点:
明确设计要求
使用环境分析:确定防爆箱的应用场景,如煤矿井下、石油化工车间、面粉厂等,不同环境的爆炸危险介质和危险程度不同。例如,煤矿井下主要存在甲烷等气体,而石油化工车间可能有多种易燃易爆气体和蒸汽。
防爆等级确定:根据使用环境中的爆炸性物质类型、级别和组别,依据相关标准如 GB 3836 系列标准,确定防爆箱所需的防爆等级,包括设备类别(如 Ⅰ 类、Ⅱ 类、Ⅲ 类)、气体组别(如 ⅡA、ⅡB、ⅡC)和温度组别(如 T1 - T6)。
电气参数规划:明确防爆箱内电气设备的电压、电流、功率、频率等参数,以及所需的回路数量、接线方式等,确保电气系统的匹配和安全。
结构设计
外壳设计
材质选择:根据防爆要求和使用环境,选择合适的材质,如铸铝合金、不锈钢、碳钢等。铸铝合金具有良好的铸造性能和较轻的重量,适用于一些对重量有要求的场合;不锈钢则具有的耐腐蚀性,适用于恶劣腐蚀环境。
强度计算:对防爆箱外壳进行强度计算,考虑可能承受的爆炸压力、外部机械冲击等因素,确定外壳的厚度和结构形式,以在危险情况下外壳不会破裂或变形。
外形尺寸:根据内部电气元件的布局和安装要求,以及使用现场的空间限制,确定防爆箱的外形尺寸,同时要考虑操作和维护的便利性。
隔爆结构设计
隔爆面设计:对于隔爆型防爆箱,要设计合理的隔爆面,包括隔爆面的间隙、宽度、粗糙度等参数。隔爆面间隙应根据防爆等级严格控制,一般在 0.1 - 0.5mm 之间;隔爆面宽度则根据外壳容积和防爆等级确定,通常在 12.5 - 40mm 范围内。
紧固方式:采用合适的紧固方式,如螺栓连接,确保隔爆面在爆炸压力下仍能保持良好的密封性和稳定性。螺栓的数量、直径和间距等都要经过计算和设计。
内部布局设计
电气元件布置:根据电气原理和操作流程,合理布置内部的电气元件,如断路器、接触器、继电器、熔断器等,确保元件之间有足够的电气间隙和爬电距离,避免相互干扰和短路。
布线设计:规划好电线电缆的走向和固定方式,采用阻燃、耐油、耐腐蚀的电缆,并确保布线整齐、有序,便于安装和维护。
性能设计
散热设计:考虑电气元件在运行过程中产生的热量,设计有效的散热措施,如增加散热片、开设通风孔、安装散热风扇等。通风孔要采取防护措施,防止外界灰尘和杂物进入。
防护设计:根据使用环境,设计合适的防护等级,如 IP54、IP65 等,以防止灰尘、水等进入防爆箱内部,影响电气设备的正常运行。通常采用密封胶圈、密封垫等进行密封。
接地设计:设置可靠的接地系统,确保防爆箱在发生漏电等故障时,能够迅速将电流导入大地,保障人员和设备的安全。接地端子应具有足够的导电性和机械强度。
人性化设计
操作与维护便利性:在设计时要考虑操作人员的操作习惯和维护需求,设置易于操作的开关、按钮、指示灯等,方便操作人员进行操作和观察设备运行状态。同时,要预留足够的空间和通道,便于维护人员进行检修和更换电气元件。
标识与警示:在防爆箱表面设置清晰、醒目的标识和警示标志,如防爆标志、危险警示标志、操作说明、接地标志等,提醒操作人员注意安全事项,正确使用和维护防爆箱。
设计验证与优化
建模与仿真:利用计算机辅助设计(CAD)、计算机辅助工程(CAE)等软件,对防爆箱的结构和性能进行建模和仿真分析,如强度分析、热分析、流场分析等,验证设计的合理性和可靠性,及时发现问题并进行优化。
样机制作与测试:制作防爆箱样机,进行实际的性能测试和防爆试验,包括隔爆性能测试、电气性能测试、防护性能测试等,根据测试结果对设计进行进一步的优化和改进,确保防爆箱满足设计要求和相关标准。
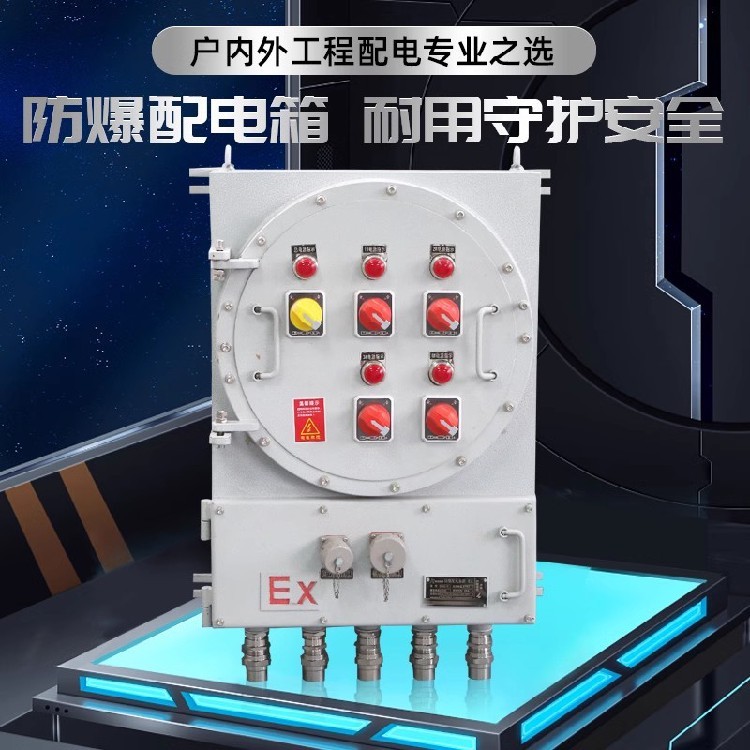
防爆箱的防爆等级
防爆箱的防爆等级是根据相关标准,从设备类别、气体组别、防爆型式等多方面进行划分的,以下是具体介绍:
按设备使用类别划分
Ⅰ 类:适用于煤矿井下用电气设备。
Ⅱ 类:用于除矿井外其他场合使用的电气设备,Ⅱ 类又可细分为 ⅡA、ⅡB、ⅡC 三类。ⅡA 类对应的大试验安全间隙 MESG 大于等于 0.9 且小点燃电流比 MICR 大于 0.8;ⅡB 类对应 0.5<MESG<0.9 且 0.45≤MICR≤0.8;ⅡC 类对应 MESG 小于等于 0.5 且 MICR 小于 0.45。ⅡC 类的防爆要求高,可适用于 ⅡA、ⅡB 的使用条件。
Ⅲ 类:用于除煤矿以外的爆炸性粉尘环境电气设备,Ⅲ 类还分为 ⅢA、ⅢB、ⅢC 类。ⅢA 类适用于可燃性飞絮;ⅢB 类适用于非导电性粉尘;ⅢC 类适用于导电性粉尘。
按爆炸性气体混合物引燃温度分组
分为 T1 至 T6 六组,具体如下:
T1:引燃温度 450℃。
T2:引燃温度范围为 300℃<t≤450℃。
T3:引燃温度范围为 200℃<t≤300℃。
T4:引燃温度范围为 135℃<t≤200℃。
T5:引燃温度范围为 100℃<t≤135℃。
T6:引燃温度范围为 85℃<t≤100℃。
按防爆型式划分
Ex d(隔爆型):通过坚固的外壳将内部电气设备与外部爆炸性气体隔离,当内部发生爆炸时,外壳可以承受爆炸压力,并防止火焰和热量传到外部,适用于存在 IIB、IIC 级别爆炸性气体环境。
Ex e(增安型):通过增加电气设备的安全性,避免设备在正常或非正常工作状态下产生火花或高温,从而避免引发爆炸,适用于存在 IIC 级别爆炸性气体环境。
Ex i(本质安全型):确保电路在任何故障情况下,产生的能量都不足以引燃爆炸性气体混合物,适用于各种危险环境,尤其是需要频繁维护和检查的场所。
Ex p(正压型):通过向设备内部充入保护性气体(如氮气),并保持正压,防止外部爆炸性气体进入设备内部,适用于存在 IIA、IIB 级别爆炸性气体环境。
Ex n(无火花型):确保电气设备在正常运行条件下不会产生火花和高温,适用于存在 IIA 级别爆炸性气体环境。